Understanding Put Shack: A Comprehensive Guide
Put shack is a term that may not be familiar to everyone, but it holds significant importance in various contexts, especially in the realms of construction and logistics. This article aims to provide an in-depth exploration of what a put shack is, its applications, and the impact it has on different industries. Throughout this discussion, we will delve into the functionalities, advantages, and key considerations when utilizing a put shack in your operations.
The concept of a put shack has gained traction in recent years due to the increasing demand for efficient space management in both industrial and commercial settings. As businesses strive for optimization, understanding the nuances of a put shack becomes essential. In this article, we will break down the various components of a put shack, highlighting its relevance and how it can be leveraged for better operational efficiency.
By the end of this article, readers will have a clear understanding of what a put shack entails and how it can be integrated into various workflows. We will also provide practical tips and insights to ensure you can maximize the benefits of utilizing a put shack in your business operations.
Table of Contents
What is Put Shack?
A put shack, in essence, refers to a designated area within a warehouse or storage facility where items are organized, sorted, and prepared for distribution. This area plays a crucial role in inventory management, allowing businesses to streamline their processes and enhance efficiency.
Typically, a put shack is equipped with various tools and equipment that facilitate the sorting and organizing of goods. These may include shelving units, bins, and labeling systems that help employees quickly locate and handle products. The design and layout of a put shack can vary based on the specific needs of a business, but its primary function remains the same: to optimize space and improve workflow.
Key Features of Put Shack
- Designated space for sorting and organizing inventory.
- Enhanced visibility and accessibility of products.
- Integration with inventory management systems.
- Flexibility to adapt to changing business needs.
History of Put Shack
The concept of a put shack has evolved over time as industries have embraced more efficient inventory management techniques. Initially, businesses relied on conventional storage methods, which often led to disorganization and inefficiencies. However, with the advent of modern logistics and supply chain management practices, the need for specialized areas like put shacks became evident.
As technology advanced, the implementation of put shacks became more sophisticated. Today, many organizations utilize automated systems and software that integrate seamlessly with their put shack operations, allowing for real-time tracking and management of inventory.
Applications of Put Shack
Put shacks find applications across various industries, including but not limited to:
- Retail: In retail environments, put shacks are essential for managing stock, especially during peak seasons.
- Manufacturing: Manufacturing plants utilize put shacks to organize raw materials and components efficiently.
- Logistics: Logistics companies depend on put shacks for sorting and preparing shipments.
- Food and Beverage: In the food industry, put shacks help in managing inventory while ensuring compliance with safety regulations.
Advantages of Using Put Shack
Implementing a put shack offers several advantages for businesses, including:
- Improved Efficiency: Streamlined sorting and organizing processes lead to faster inventory turnover.
- Better Space Utilization: A well-designed put shack maximizes storage space, allowing for more effective use of the facility.
- Enhanced Accuracy: Minimized errors in inventory management due to organized workflows and clear labeling.
- Cost Savings: Reduced labor costs and improved operational efficiency translate to financial savings for the business.
How to Implement Put Shack
Implementing a put shack in your operations requires careful planning and execution. Here are some steps to guide you:
Best Practices for Using Put Shack
To make the most out of your put shack, consider the following best practices:
- Regular Audits: Conduct regular audits to ensure inventory accuracy.
- Utilize Technology: Implement inventory management software to enhance tracking and organization.
- Maintain Cleanliness: Keep the put shack clean and organized to prevent accidents and improve efficiency.
- Encourage Feedback: Solicit feedback from employees to identify areas for improvement.
Case Studies and Examples
Several companies have successfully implemented put shacks, resulting in significant improvements in their operations. For instance:
- Company A: After implementing a put shack, Company A reduced its inventory processing time by 30%.
- Company B: The introduction of a put shack led to a 20% decrease in errors during order fulfillment for Company B.
Conclusion
In summary, a put shack is an invaluable asset for businesses looking to optimize their inventory management processes. By understanding the key features, applications, and advantages of a put shack, organizations can enhance their operational efficiency and reduce costs. We encourage readers to consider how a put shack can be integrated into their workflows and to share their experiences in the comments below. Don’t forget to explore other articles on our site for more insights on improving your business operations.
Thank you for reading! We hope you found this guide on put shack informative and valuable. We invite you to return for more articles that explore various topics relevant to your interests.
Also Read
Article Recommendations
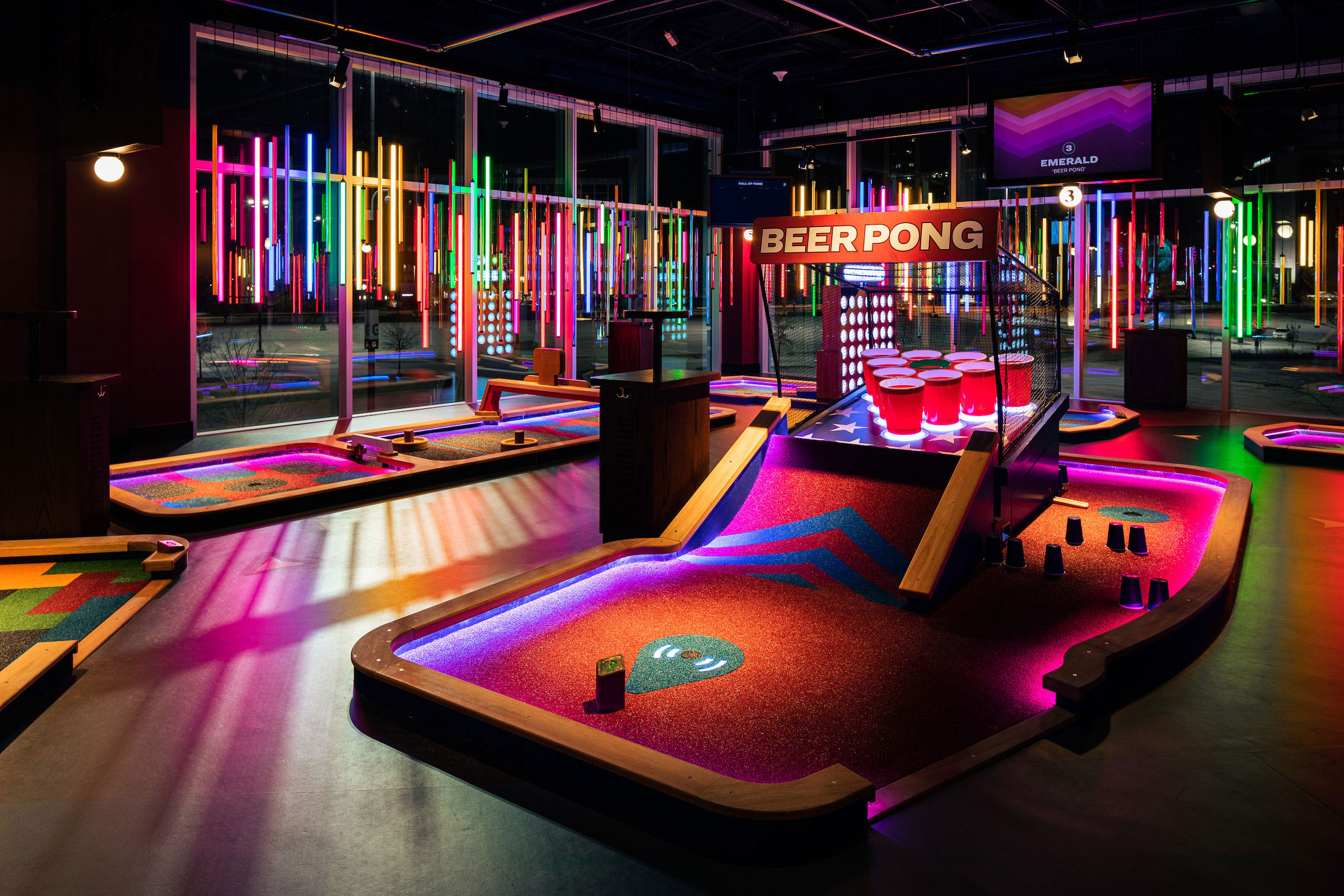
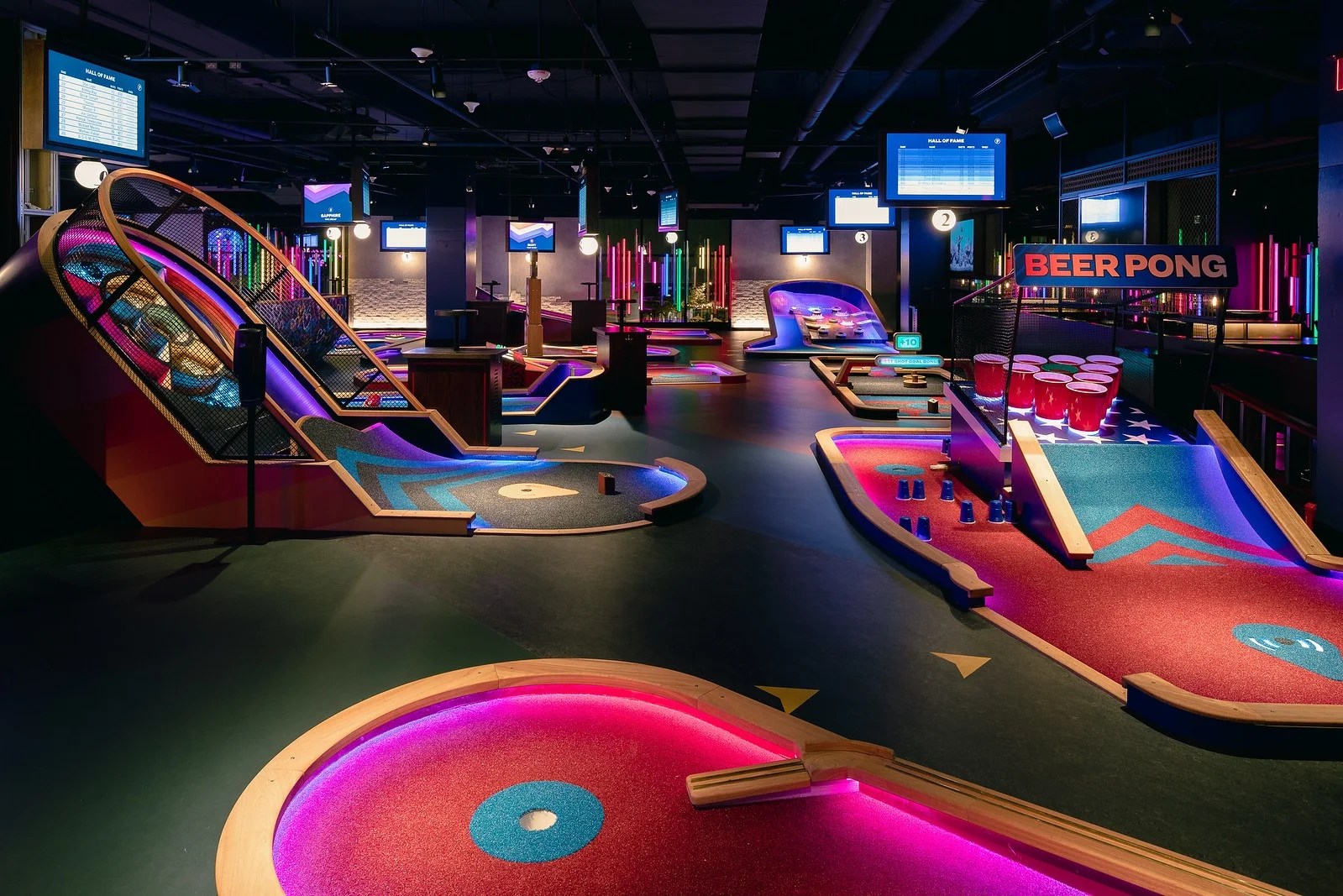
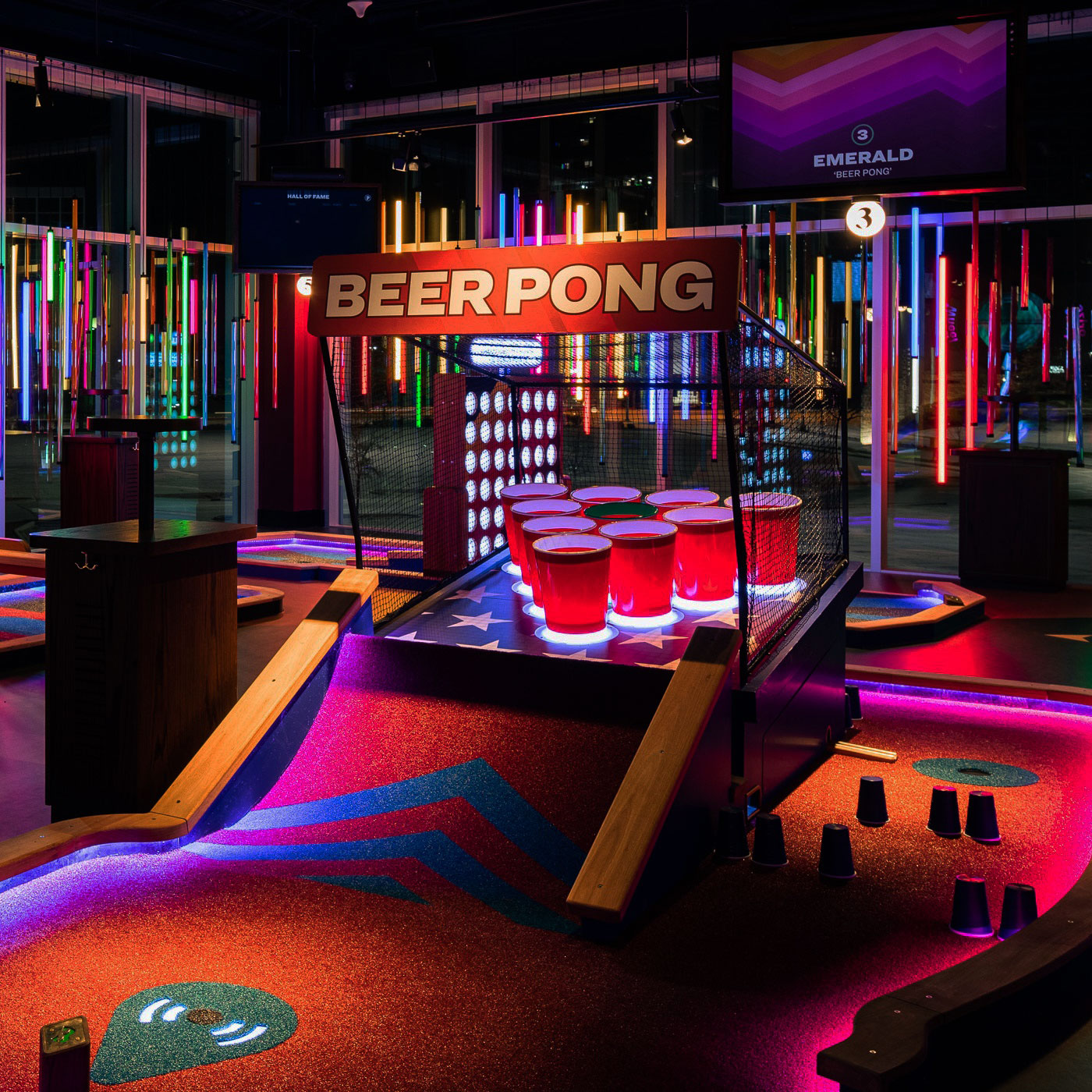
ncG1vNJzZmivp6x7tMHRr6CvmZynsrS71KuanqtemLyue9Oop6edp6iBcLzUrWSsoJGYuG%2B006aj